Dangerous Decks
This deck had a big problem! Fortunately, most of the deck problems we see are not nearly as severe. The methods and materials of deck construction are pretty much out of the consciousness of most people until you hear about a catastrophe, like the porch failure in Chicago that killed 12 people in 2003. Its actually common to find at least a couple of local stories of deck failures, with some injuries, each year. These typically occur when a party is in progress that concentrates numbers of people on a deck with problems. Teens and graduations are just right for causing trouble.
Most building codes and practices are designed to provide safety to the people in or on a structure. Design criteria have to address worst case scenarios. This is the key reason for deck dangers. When amateurs build decks, they don’t usually anticipate what may eventually take place on the beautiful project they are laboring to complete.
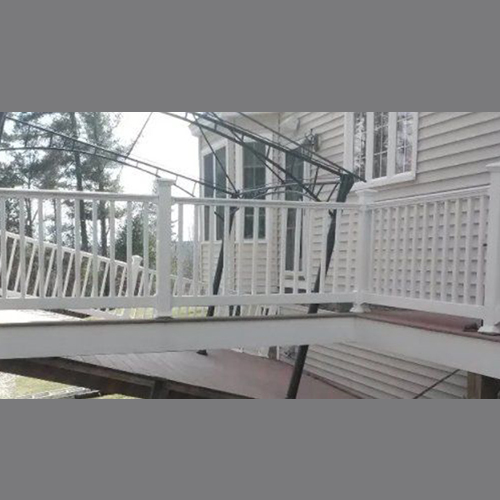
Standard deck construction calls for a 40 pound per square foot live load. Imagine a nice rectangular deck on a townhouse that is 16 feet against the house, comes out 12 feet into the back yard, and is elevated 9 feet above the ground. That’s 192 sq. ft. at 40 per sf which comes up to a mere 7680 lbs. of potential weight. That’s a couple of cars!!
Let’s be more conservative and guess that when the next lunar eclipse shows up you’re throwing a moon party. At 10:25 PM, you and your 20 guests file out to the deck to watch the show. We’ll guess you have 21 people at an average of 160 lbs (young, old, male, female, in shape mostly). Hey, that’s only a bit over a ton and a half at 3360 lbs. With a 2’x2’ space for each, they are only taking up 84 of the 192 sq.ft. If they are evenly distributed, the deck will feel the least stress. Imagine concentrating them into a smaller area or if they move as a group, or all lean against the railing to catch a glimpse of the streaker.
I think you get the point that under the right conditions, decks are elevated platforms that support huge loads. They had better be able to stand firm! That’s why good inspectors pay very close attention to decks!
Typical trouble spots
- Attachment to the House – Most decks are rectangles with floor joists perpendicular to the house. One end supported by posts and a beam, the other is attached to the house framing. Typically, there is a “ledger board”, which is attached to the house band board and supports the joists. The attachment of this board is what failed in the first picture. During home inspections, I have found many of these boards simply nailed to the house. They must be “through bolted”. Some decks are bolted but only partially. Some decks are bolted in a straight line that has a crack in the ledger board connecting each bolt hole. Some are attached to a brick wall with lag screws and lead shields. There are times when the deck is attached with lag screws that are screwed into ½” plywood sheathing only! Suppose Uncle Fred “Lagged” the ledger board to the house. He used 3/8 ” Lag Screws at 3 1/2″ long. He figured that he had to go through a 1 1/2″ pressure treated board and then completely into another 1 1/2 ” board inside the house framing (behind the vinyl siding). Well Uncle Fred didn’t know that there was a 1″ layer of foam sheathing covering the house frame. So maybe he anchored this multi- ton platform by having about 1/2″ of the tapered tips of the lag screws into real wood and the rest in Styrofoam!
- Railings and their Supporting Posts – So you have a nice raised platform (a deck), but how do you keep your guests from falling off of it?? You put up a railing, of course. By today’s standards, the railing has to be a minimum of 36″ high with no more than 4″ gaps in the surrounding enclosure. You are supposed to be able to exert a 200 lb. lateral force perpendicular to the railing, at any point on the railing. ( HA! HA! HA!)Through the years I have knocked hundreds of balusters ( the vertical pickets) loose with a light hit of the toe or my fist. Most balusters are 1 1/2″ thick. Most are nailed from the outside of the deck into the frame(#1). This is often done with 2″ nails. So 1 1/2″ of the nail is through the baluster and 1/2″ is into the wood that is really securing it. Balusters should be screwed into the frame with a screw that can penetrate the frame as deeply as possible without emerging from the back side. Preferably, balusters should be attached inside out, that is, from the inside of the deck screwed to the frame such that a person pushing the baluster is pushing it against the deck frame and not simply against the screw. The top rail board is what makes you feel secure, but flimsy balusters can certainly be a safety concern with children. Besides the various miss-attachments, the baluster itself is frequently defective. Many have large knots that are weak points. Some are very small, lathe turned pieces, that barely withstand a few pounds of pressure without snapping.
- Posts – are typically 4X4 pressure treated pine that have the tough job of keeping the railing assembly secure. Many of these posts are notched 50% and bolted to a single framing joist. Some are screwed in with drywall screws and some are simply nailed. Through bolting is better but still frequently poor due to the bolt placement. Bolt a railing post to a flexible point of anchorage and you get a flexible railing. Almost all decks have at least some inadequate posts. If you test them scientifically, (an engineer will stress a post with a 500 lb lateral force for a 250 % safety margin), they almost all fail. Posts that are solid into the ground and extend above deck level as railing posts would be the exceptions. Another solution is to use specialty post anchors from a manufacturer like “Simpson Strong Tie”. These specialty anchors are vastly superior to simple bolting. Nailing is laughable!
- Racking – is the lateral movement of a structure. In the case of a deck, it is typically a side to side sway that is parallel to the wall of the house to which the deck is attached. If you think of the deck surface as the top side of a rectangle with the 2 vertical posts as the sides and ground as the 4th side, racking is the tendency of this rectangle to be changed into a parallelogram (see my stick diagram). That can be bad. My scientific method for assessing this is to shake my butt! That is, I go to the point farthest from the house and swing my hips side to side. Good decks won’t move or maybe have a slight vibration. However, many will move 2″ or 3″ side to side. Some of my Realtor friends won’t get on the deck with me any more when I start my motion. Some clients quickly head for the sliding doors or pin themselves up against the house. I do enjoy the drama a bit, but if I can induce enough movement in a deck to literally scare people, their fears are actually quite justified. Decks that will sway readily may well come down! I’m no lightweight, but I’m just a single body. Just imagine what 10 or 20 rocking teenagers might do. The good news is that racking is pretty easily remedied. The most effective way to resist the racking force is to install braces at 45 degrees between the vertical posts and the perimeter joist. These attachments must be firmly anchored. What that does is to take a rectangle and make triangles where posts meet deck. Triangles are the building blocks of towers cranes bridges etc. because they provide rigidity. The rectangle won’t become a parallelogram. Posts that extend into the ground can also provide lateral stability. Decks that wrap around a house corner are good because the house resists the motion. Stairs (parallel to house) will provide security because the stair stringers become a lateral braces when anchored to ground at bottom and deck floor at top.
- A Note on Footers – Footers are a basic of construction but are really a minor concern in relation to decks. Size and depth of footers are very important to house construction because of the weight involved and the fact that sags and movements skew doors, crack windows, make floors unsightly, may ruin brick veneers, and in some cases cause huge problems. With decks, the name of the game is “prevent catastrophe”. Don’t let the deck fall off of the house; don’t let a child go through the guard rail; don’t let the railing be pushed over; and don’t have the deck swinging back and forth when your friends are crowding onto it. Footer issues cause very slow sags that can easily be fixed. So don’t worry too much if your contractor digs a hole for a footer that’s a few inches shy of the frost line. But do make him attach the post base to the footer! There are several different metal brackets or straps that provide a positive connection between posts and ground. Some posts have “Kicked out” under stress. This is especially likely in a deck with a lot of racking. Some posts are raised off the surface or slab by little metal feet. (This is not a bad idea in that pressure treated wood does rot. Parts don’t get the full chemical treatment and rot. Some of the PT wood I have used for ground contact landscaping now looks like Swiss Cheese.) If the posts are on raised feet, the feet must be attached to posts and footer firmly, with some sort of bracket. This is easily done but omitted frequently. Many 10-15 year old decks are supported by posts that simply rest on the patio slab below. I can often kick these with my foot and make them move.
Solutions
- Specify a deck that could be “free standing”. A free standing deck will have an extra couple of posts and a beam near to the house. The deck frame is still attached to the house to add stability, but the posts carry the vertical load, not bolts, nails or screws. This will add only a small additional cost and completely eliminates the dangers demonstrated in the first photo. Many good contractors already use this technique and many municipalities require it.
- Hire a pro! Besides getting estimates from several contractors, you should get license numbers, pictures of 4 or 5 of their previous jobs, and references. Proposals should be written with specifics about the size and materials used. Most localities now require a building permit for a deck. Contracts should state specifically that the deck is being built to the current required standards and that permits are included. If there are no standards in your area, you’d better do the research or hire someone to specify the details, (like how it will be attached to the house).
- If you do it yourself, you had better be confident of the details. Some homeowners can build decks that are stronger than the pro models. They usually overbuild and waste materials but the finished product can be excellent. Don’t let Uncle Fred do it unless you’ve interviewed him on experience and construction details and you feel lucky.
P.S. Decking recall
Most Pressure treated decking will last 20+ years if it is not subject to ground contact. Non PT wood will probably rot in spots within 10 years. Keeping the surface treated will always extend life. Cedar is better than non-treated wood, but is only rot resistant, not rot proof. The new composite materials that provide “maintenance free” surfaces are building materials that have not yet been time tested. One lesson I have taken from many years of doing this is simply that you can’t judge a building product until its been around for a few (say 20) years. Here’s a recall link for a relatively new decking material sold lightly in PA and probably not at all in MD. http://www.deckingnotice.com/